|
Post by rnagle on Mar 13, 2014 18:14:27 GMT -8
We went easy on 'em - the fellows were only there until shortly after 11:00!  I (and one of the lads helping instruct) brought the tanker and reserve pumper down from our other station about 10+ minutes away, so we had to drive them back, rinse (winter in Ontario = salt & dirt) and finish paperwork. Then drive the 10+ minutes home (yawn) =.......midnight!  I'm sure there was some griping about the late evening (our scheduled training time is from 7:00 to about 9:30 on average), reality is with some trainings (rural pumping especially) there is a lot to do, a lot to set up and a lot to clean up. No point in running half a training, if anything I see a real need for more practice, not less. Turnout actually wasn't bad, 19 active members, 11 attended. 1 trained at a different station last week due to their work schedule, 2 for sure and likely 1 more will attend daytime training on Saturday March 29. That only leaves 4 possible "no shows" who didn't want to do the slugging! And since we trained at Stations 1 and 2 the previous week, and the same group of us ran it at all 3 stations, there was plenty of time for word to spread about how late it ran.  Only problem is, that meant I didn't get home until midnight+ 2 evenings last week....... 
|
|
|
Post by trailking120 on Mar 13, 2014 18:22:58 GMT -8
Sounds the same. I always have a few that seem to just slip through the fold when we are cleaning the equipment. 
|
|
|
Post by rnagle on Mar 14, 2014 19:37:18 GMT -8
Oh, we aren't the only ones with that problem?  One of the mundane little detail parts that just about every truck has these days, convex spot mirror. Tried a little different approach with this one, using 1/4" disk punched from .010 brass sheet. Strip .040 wide cut from same sheet bent for mounting bracket & soldered in place. Two nut/washer castings simulate fasteners, drop of epoxy on face gives proper convex surface. Will Alclad for reflective surface, on this truck mirror body itself was black: 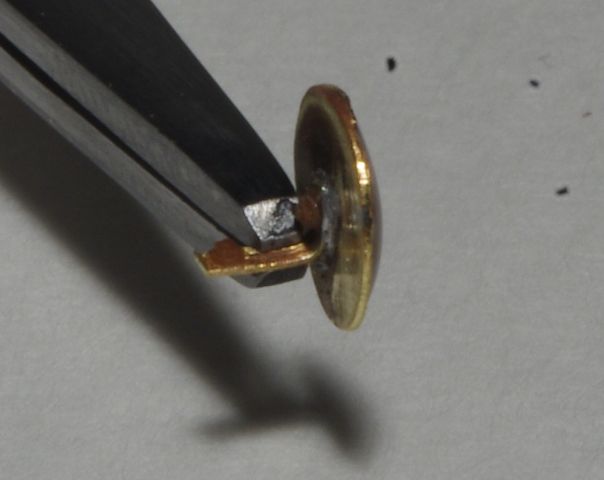
|
|
|
Post by gatorincebu on Mar 15, 2014 3:47:35 GMT -8
Oh, we aren't the only ones with that problem?  One of the mundane little detail parts that just about every truck has these days, convex spot mirror. Tried a little different approach with this one, using 1/4" disk punched from .010 brass sheet. Strip .040 wide cut from same sheet bent for mounting bracket & soldered in place. Two nut/washer castings simulate fasteners, drop of epoxy on face gives proper convex surface. Will Alclad for reflective surface, on this truck mirror body itself was black: 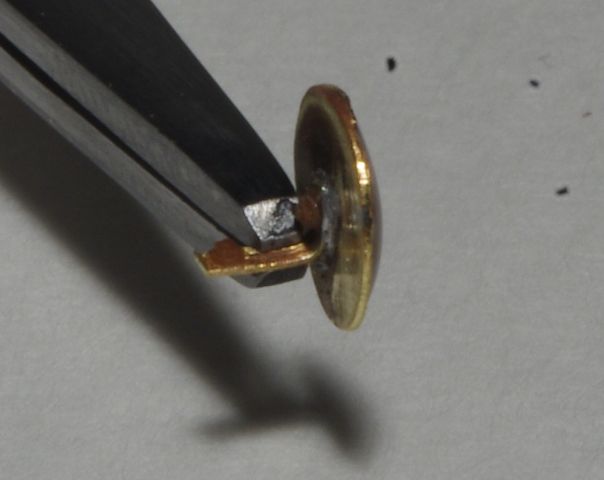 Dayum!!!!!!!!!!!!!!!!!!!!!!!!!!!!!!!!!!!!!! Good idea!!!!! Be Well Gator
|
|
|
Post by rnagle on Mar 19, 2014 18:01:55 GMT -8
Slowly getting there, mudflaps made from .015 styrene sheet & strip with 1/32" square brass bar hangers. .005" shim brass cut to strips .060 wide soldered to square bar where flap bolts to hanger, Tichy Train Group bolt heads attached with ACC. Bracket on frame is piece of 1/16" square brass tube soldered to 1/64" brass strip, drilled & pinned to frame: 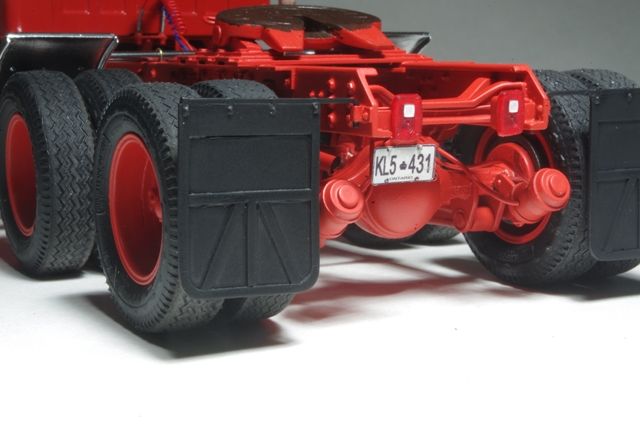 Cab interior mostly stock, low back seats from Titan/90 kit used with backs filled in. Free standing details added include window cranks, door pull straps, door handles (taken from "snap" Pete 359 kit sleeper, shifter from that kit also used), toggle switches and brake knobs. Floor mat is scribed styrene sheet. 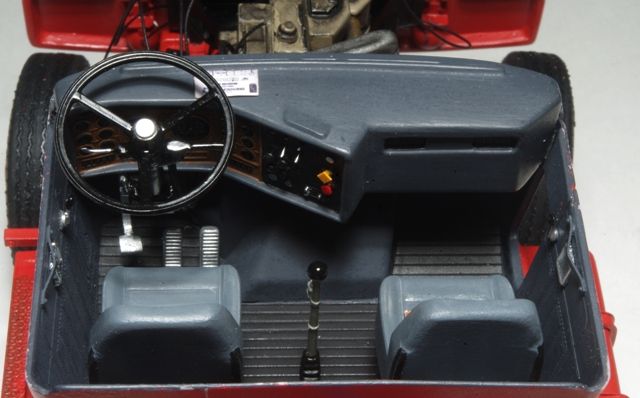 Cab & hood set in place, still lots to do yet in the way of "fiddly bits" but looking like a truck. Detail Master photetched grille used. 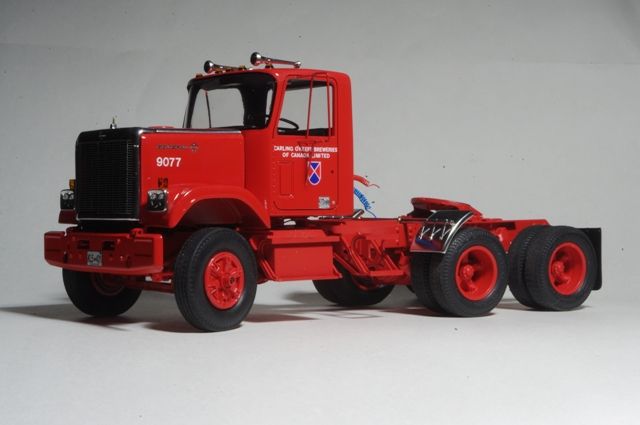
|
|
|
Post by jimb on Mar 19, 2014 19:20:40 GMT -8
Fantastic details. Absolutely fantastic.
|
|
|
Post by gatorincebu on Mar 20, 2014 3:58:06 GMT -8
Robert, That is really taking shape now! looks real good.
Be Well Gator
|
|
|
Post by rnagle on Mar 24, 2014 17:02:37 GMT -8
Thanks gator, some more small fiddly items completed, especially under the hood. Kit air intake piping wouldn't work as engine was changed to a Cummins, aluminum tube and pieces of intake piping from 2 of the "snap" 359 kits used. Rad braces are .035 styrene rod. 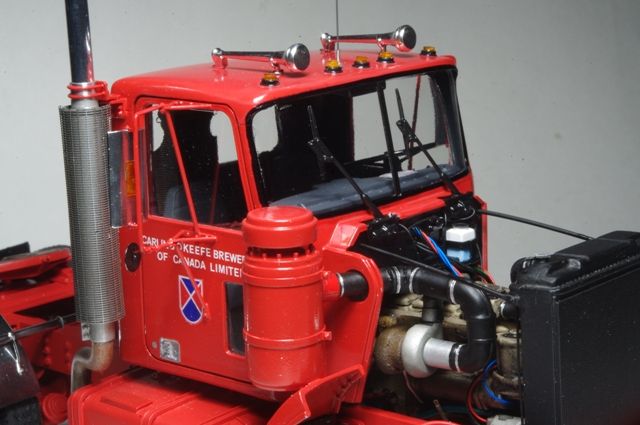 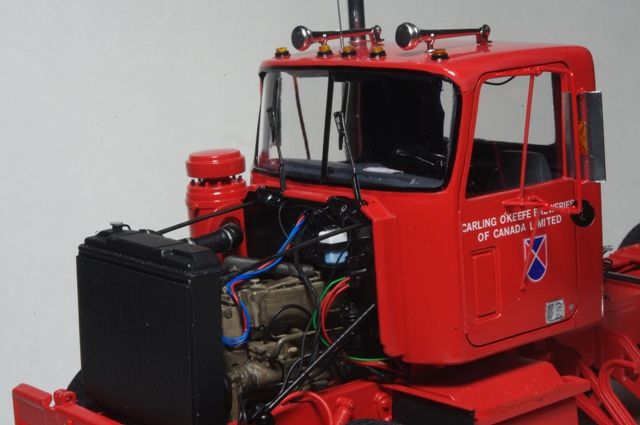 Out back, Plaskit's glad hands and electrical plugs made adding trailer hook up easy, lines themselves are 30 gauge coloured wire coiled around 1/16" rod. 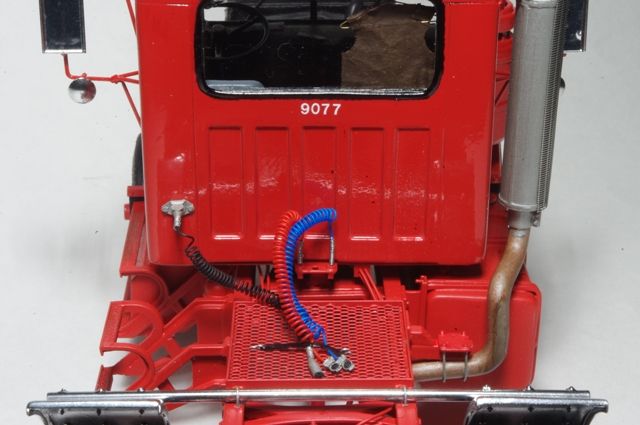
|
|
|
Post by rnagle on Mar 25, 2014 18:44:10 GMT -8
Mix of plastic kit parts & scratchbuilt brass ones: Grab handles are kit parts cut free from stack, drilled for .016 brass wire pins. 1/64 x 1/16 brass flat bar bent to match stack, drilled in centre to fit over pin. Stack and heat shield drilled to match, grab handle will receive Alclad chrome. Pins will ensure good solid connection once assembled. 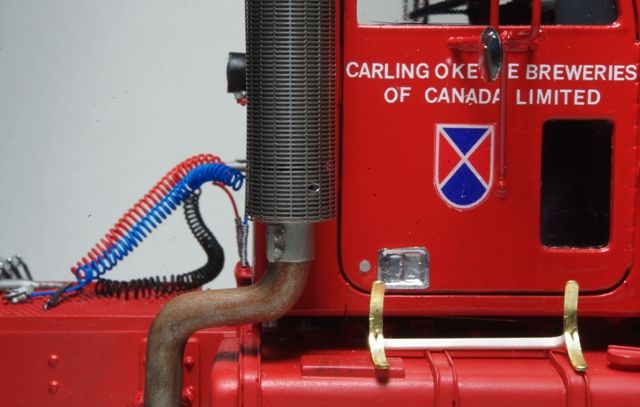 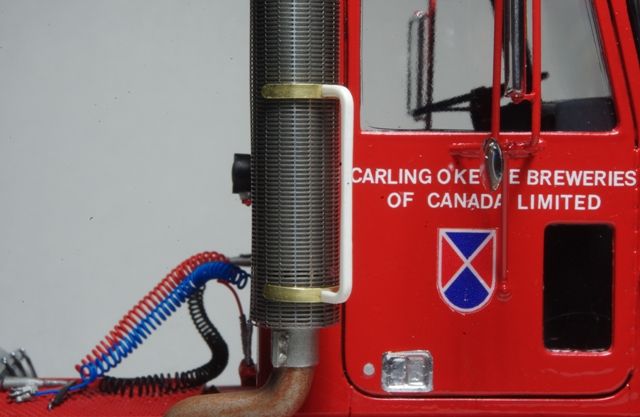
|
|
|
Post by gatorincebu on Mar 25, 2014 19:25:48 GMT -8
QQ........................ dayum!!!! What will you think of next?
Be Well Gator
|
|
|
Post by Robert Myers on Mar 26, 2014 9:26:18 GMT -8
That is looking excellent!!!
|
|
|
Post by rnagle on Apr 2, 2014 14:40:56 GMT -8
Thanks guys! Last of the "fiddly bits" finally done, once hood was installed stop cables made using black thread. Craft wire coiled to make spring, HO scale diesel locomotive lift rings (formed wire eye bolts) used for attachment points to rad & hood: 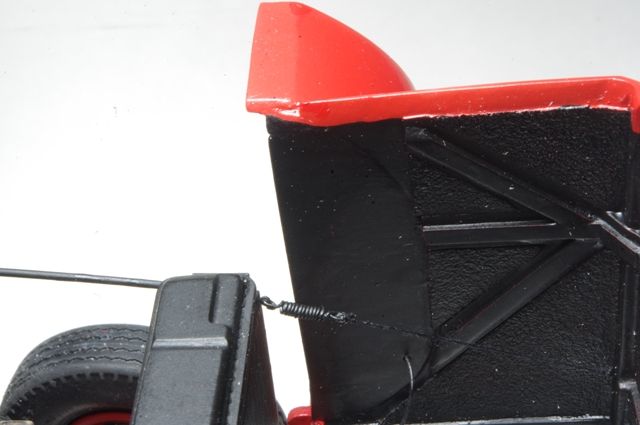 Hood latches also required, "nose job" to shorter BBC removed them however kit parts molded to hood are so shallow paint would have obscured them anyway. Styrene strip and short piece of .020 brass wire used to make replacements. Wire left extra long & cab drilled so latch is pinned in place, otherwise miniscule glue joint would have been too weak: 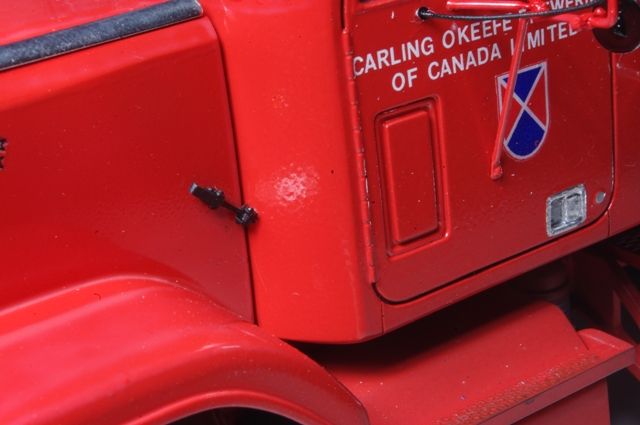 Air line dummies, worklight and grease for the fifth wheel! (Dummies not in use because a trailer is pending  ) 
|
|